Staff Profiles
National Hospital Week – Honoring Our Materials Management Department
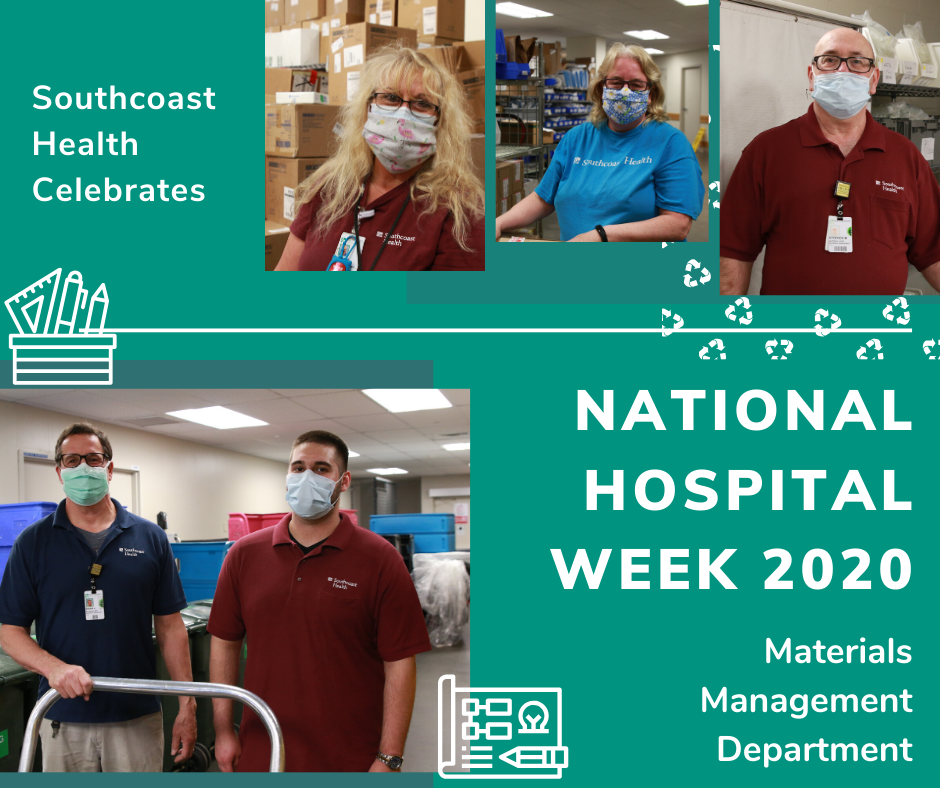
A hospital system functions on a variety of commitments, never faulting. The duties of hospital personnel are both from clinical staff who heal us and our essential staff who ensure that our hospitals and facilities are fully-functioning and serving our community to its highest degree. During Hospital Week, we highlight our Materials Management Department.
Like electricity through the walls or blood cells through the body, needed materials and supplies move through the Southcoast Health system to and from every building, department and unit, every day of the year. This includes any kind of imaginable material – office supplies, cleaning supplies, equipment, food, mail, medications, lab specimens, instrumentation, blood, X-rays, signage and more. And, of course, personal protective equipment (PPE): gowns, shoe covers, masks, face shields.
A team of 22 couriers and one dispatcher – as well as a fleet of 14 vehicles – make about 10,000 deliveries monthly, says Mike Correia, Director of Materials Management, Distribution and Logistics. That translates into thousands of individual items, all critical to a well-functioning Southcoast.
“We’re doing pickups and deliveries all day long. We added delivery routes to accommodate the new Buttonwood facility, the UMass Dartmouth Field Hospital and our COVID-19 testing site,” Correia says.
Once delivered, these goods are checked in with scanning devices, stored temporarily and distributed by just under 30 staff in Materials Management.
“Our main concern is to make sure everything Southcoast needs gets delivered to where it’s needed – from ERs to ORs – in a timely fashion,” says Correia, who has been with Southcoast for 27 years. It’s the three Rs; he explains, The Right materials to the Right place at the Right time.
The whole system operates “like a beehive,” he says, “and it hums like one because of the dedicated staff we have in the department.” With COVID-19, Graphic Arts – which produces new signage and other printed information that’s been necessary – and Materials Management have been busier than ever.
“The need for supplies has skyrocketed,” says Adam Souza, Materials Management Team Lead at St. Luke’s. “It’s been incredibly busy,” says Souza, who has been at Southcoast for 23 years. “Managing the PPE alone takes five hours of my day.” Souza, who has started his day as early as 5 am, says, “I’ve dreamt about face masks.”
“My staff have been troopers,” he says. “They’ve shined. I’ve had to delegate more, and employees have stepped up to take on more leadership tasks. When it matters, they dig in. Some have even canceled vacations to help us manage the workload.”
Bill Needham, the Team Lead at Charlton Memorial, is in his 31st year at Southcoast.
“This has been the most difficult one so far,” he says, “but everyone on my team has gone above and beyond.”
The staff have taken on new duties when necessary. For instance, because vendors have been restricted from entering the hospitals to prevent community transmission, Materials Management has been distributing office supplies from W.B. Mason, while also delivering food and milk straight to the kitchen.
Needham says he has found that everyone at the hospital is working very closely together during the crisis. “There’s a lot of community at the hospital. We’re tightly knit.”
Employees and departments are helping each other out. Just today, Needham explains, the hospital didn’t have a delivery of certain paper stock. It’s back-ordered and some departments were running out. The hospital doesn’t carry a large inventory because supplies are ordered “just-in-time,” as is done in most businesses so that valuable space isn’t taken up by excessive storage.
“We asked for two reams of paper from those who had extra, and then we redistributed the paper to those running out. I call it spreading the peanut butter on the bread,” he says. “In the end, we make sure everybody gets what they need. We also get inventive. Because of some difficulty with getting enough disposable protective gowns, we introduced washable ones from Merrow Manufacturing in Fall River.”
The COVID-19 crisis has been a learning opportunity in many ways, Needham says. “As a system, we’re learning to use materials more wisely.”